The Importance of Automotive Plastic Injection Molding in Modern Manufacturing
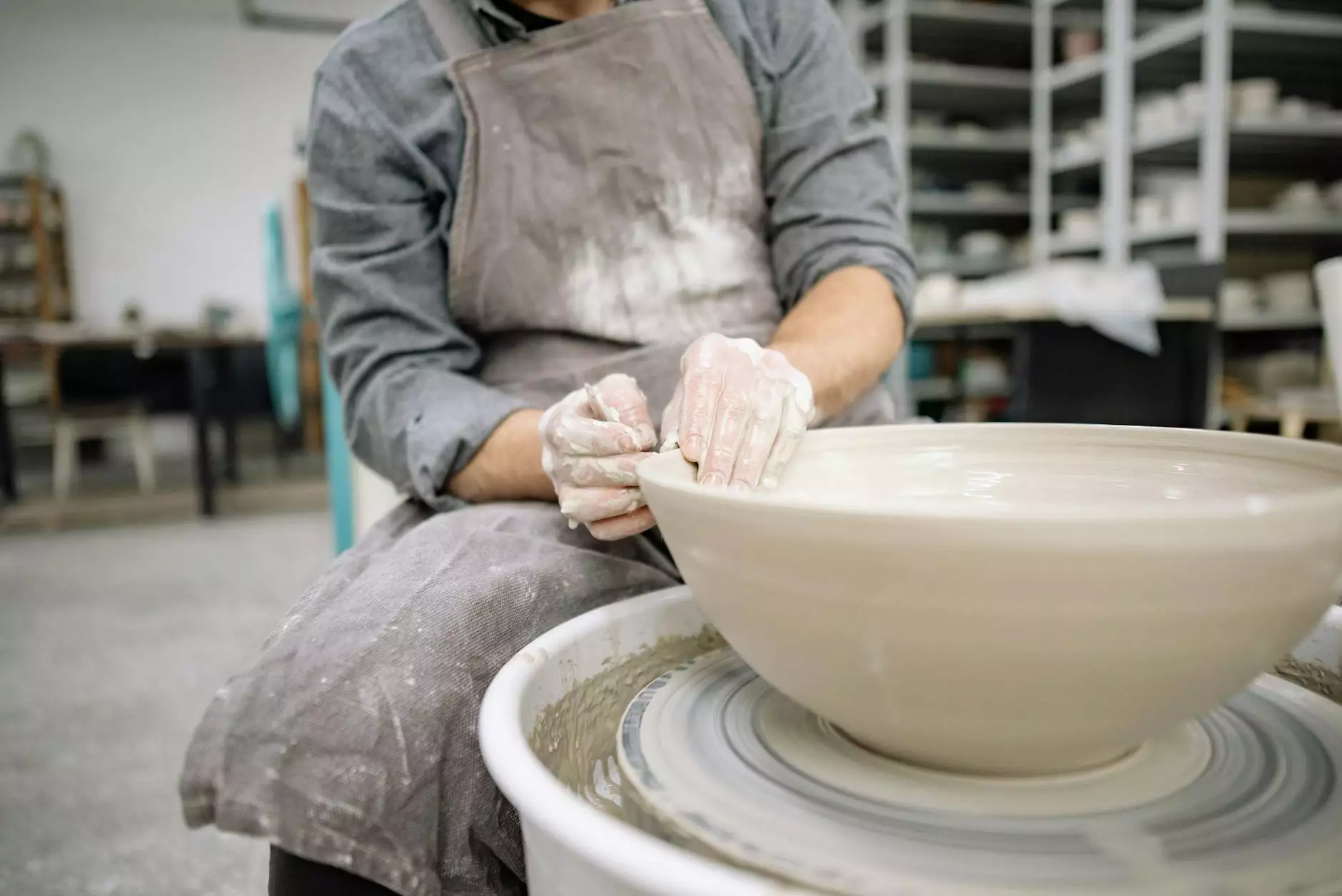
In the ever-evolving landscape of the automotive industry, automotive plastic injection molding has emerged as a crucial component of manufacturing processes. As automotive designs become more innovative and complex, the demand for efficient and cost-effective production methods is paramount. This article delves into the intricate world of automotive plastic injection molding, exploring its significance, processes, applications, and future trends.
Understanding Automotive Plastic Injection Molding
Automotive plastic injection molding refers to a specific manufacturing process that transforms raw plastic materials into finished parts and components used in vehicles. This method is renowned for its precision and adaptability, making it suitable for a wide range of applications in the automotive sector.
The Process of Plastic Injection Molding
The process of plastic injection molding involves several key steps:
- Material Selection: The first step involves choosing the appropriate type of plastic resin, which can vary based on the part's requirements such as strength, flexibility, and temperature resistance.
- Injection: The selected plastic resin is then heated to a molten state and injected under high pressure into a precisely designed mold that shapes the final product.
- Cooling: After injection, the mold is cooled, allowing the plastic to solidify into the desired shape.
- Ejection: Once the part has cooled and solidified, it is removed from the mold using ejector pins.
- Finishing: The final step may involve additional processes such as trimming, painting, or assembling to meet product specifications.
Benefits of Automotive Plastic Injection Molding
The adoption of automotive plastic injection molding offers numerous advantages to manufacturers and stakeholders in the automotive industry:
- Cost-Effective Production: Injection molding is a highly efficient process that allows for the mass production of identical parts, significantly reducing the per-unit cost.
- Design Flexibility: Designers can create intricate shapes and complex geometries that would be difficult or impossible to achieve with traditional manufacturing methods.
- Material Efficiency: Minimal waste is produced during the molding process, which aligns with today's sustainability goals within the industry.
- Durability and Performance: Parts produced through injection molding can exhibit superior strength and thermal stability, making them ideal for demanding automotive environments.
- Reduction in Assembly Time: Many components can be molded as single units, reducing the need for assembly and associated labor costs.
Applications of Automotive Plastic Injection Molding
The versatility of automotive plastic injection molding means it plays a vital role in numerous applications across the automotive sector. Some notable applications include:
Interior Components
Plastic injection molding is commonly used for producing interior elements such as:
- Dashboard panels
- Door handles
- Center consoles
- Seating components
These components not only contribute to the aesthetic appeal of vehicles but also enhance ergonomics and functionality.
Exterior Parts
Injection-molded plastic is used in various exterior automotive parts, including:
- Bumpers
- Grilles
- Body panels
- Fenders
These components must be rugged and lightweight, making them ideal candidates for injection molding.
Functional Components
Beyond aesthetics, injection molded parts often serve critical functional roles, such as:
- Fuel tanks
- Electrical housings
- Air intake manifolds
- Under-the-hood components
These require materials that withstand high temperatures, chemicals, and physical stress, which injection molding effectively provides.
The Future of Automotive Plastic Injection Molding
As the automobile industry continues to evolve, so does the role of automotive plastic injection molding. Several trends are shaping the future of this manufacturing method:
Increased Adoption of Lightweight Materials
With the global push toward improved fuel efficiency and reduced emissions, manufacturers are increasingly focusing on lightweight materials. Plastic injection molding enables the use of innovative polymers that deliver high strength-to-weight ratios, critical for modern vehicle design.
Advancements in Technology
Emerging technologies such as 3D printing, IoT integration, and automation are being integrated with traditional injection molding processes. These advancements lead to increased precision, reduced cycle times, and even greater design freedom.
Sustainability Initiatives
The automotive industry is under pressure to reduce its environmental footprint. The use of recycled materials in plastic injection molding processes and the development of biodegradable plastics represent steps toward a more sustainable future.
Challenges in Automotive Plastic Injection Molding
Despite its numerous advantages, automotive plastic injection molding is not without challenges:
Material Limitations
While many types of plastic can be molded, not all offer the necessary properties for specific applications in automotive manufacturing. The selection of the right material is crucial for achieving the desired performance and longevity of the components.
Initial Capital Investment
The setup cost for injection molding can be high due to the expense of molds and machinery. This initial investment can be a barrier for smaller manufacturers trying to compete in a technology-driven industry.
Quality Control
Ensuring consistent quality across multiple production runs is vital. Manufacturers must implement rigorous quality controls and testing protocols to maintain high standards, particularly when components are critical for vehicle safety and performance.
Conclusion: The Key to the Future of Automotive Manufacturing
In conclusion, automotive plastic injection molding is an essential manufacturing technique that supports the production of a wide range of components used in today's vehicles. The benefits it offers—such as cost-effectiveness, design flexibility, and material efficiency—make it indispensable to the automotive industry.
As the automotive landscape continues to shift with advancements in technology and sustainability initiatives, the role of injection molding will only increase in significance. By tackling the challenges head-on and capitalizing on emerging trends, manufacturers can ensure that they remain at the forefront of industry innovation.
For more information on automotive plastic injection molding and related topics, visit deepmould.net.