Fitting Lubrication: Optimizing Performance and Longevity
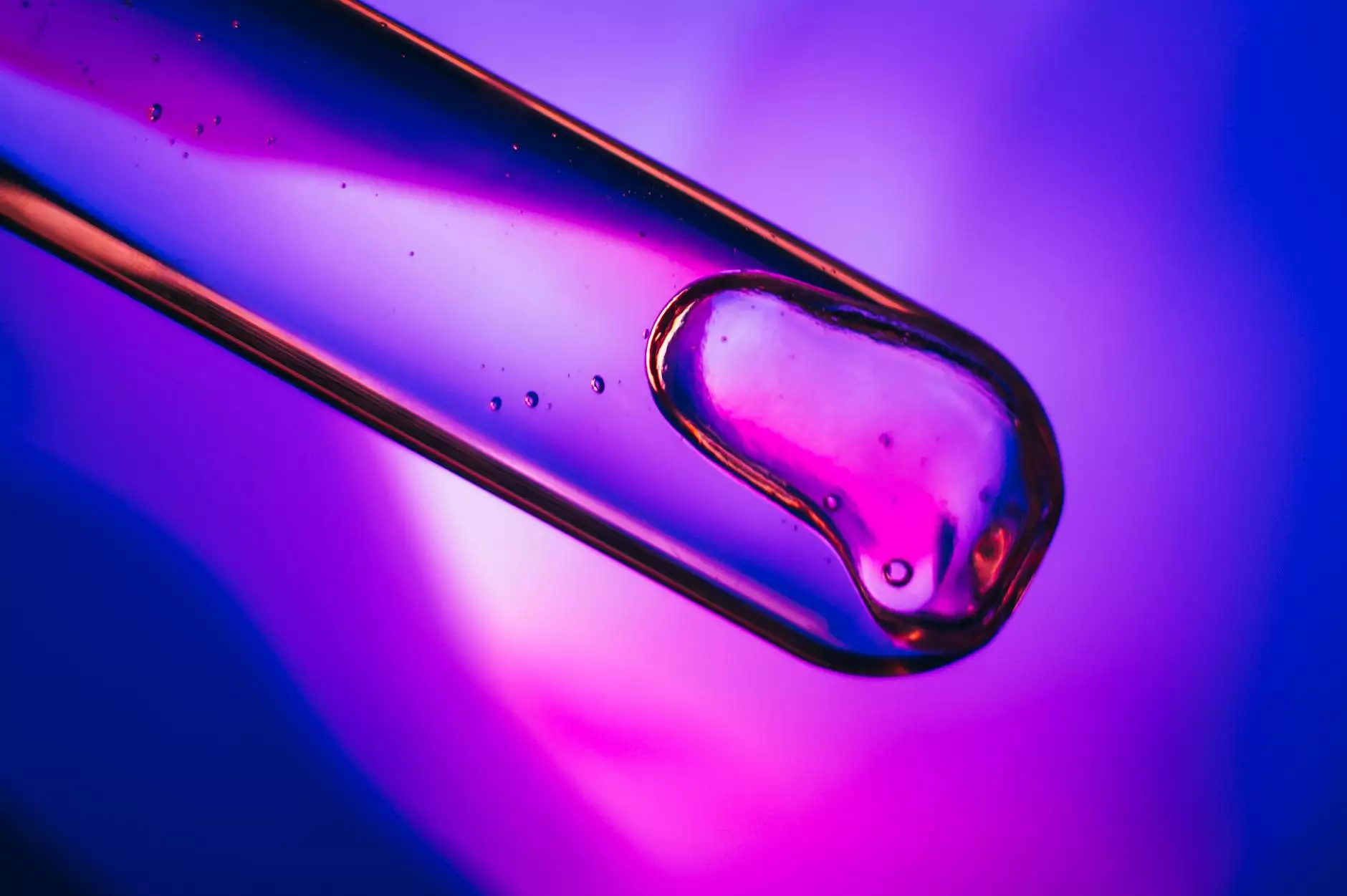
Fitting lubrication is an often-overlooked aspect of maintenance in various industrial sectors. However, it plays a critical role in ensuring the smooth operation and durability of fittings in different applications. In this comprehensive article, we will delve into the significance of fitting lubrication, its benefits, and the best practices for ensuring your fittings are always in optimal condition.
Understanding Fitting Lubrication
Fitting lubrication refers to the application of lubricants to fittings, which include pipes, valves, and connectors. These lubricants reduce friction between moving parts, facilitate smooth operation, and prevent wear and tear over time. Without proper lubrication, fittings can experience increased friction, leading to accelerated degradation and a higher likelihood of failure.
The Importance of Fitting Lubrication
The significance of fitting lubrication cannot be overstated. Here are several key reasons why it is crucial:
- Reduces Friction: Lubrication minimizes friction between moving edges, ensuring smoother operation and prolonging the life of fittings.
- Prevents Corrosion: Proper lubrication creates a barrier that protects fittings from corrosive substances, significantly reducing the risk of rust and degradation.
- Enhances Efficiency: Efficient fittings result in better flow and energy savings, which is vital in industrial applications.
- Increases Reliability: Lubricated fittings are less likely to fail, leading to increased reliability in systems which depend on them.
- Improves Safety: Properly lubricated fittings reduce the chances of accidents caused by equipment failure.
Types of Lubricants for Fitting Lubrication
Choosing the right lubricant is critical to effective fitting lubrication. Various types of lubricants are available, each suited for specific applications:
- Greases: Often used for fittings requiring longer-lasting lubrication. They are ideal for high-load applications.
- Oils: Suitable for applications needing frequent lubrication. Oils can flow into tight spaces and provide superior lubrication.
- Dry Lubricants: Consist of powdered substances that provide a low-friction layer, useful in environments where wet lubricants could be a hazard.
- Bio-Lubricants: Environmentally friendly solutions that minimize harm to the environment, often derived from vegetable oils.
Factors Influencing the Choice of Lubricant
When selecting a lubricant for fitting lubrication, consider the following factors:
- Operating Temperature: The lubricant must withstand the temperatures in which it will be employed.
- Load Requirements: High-load applications may require specialized greases to handle the stress without breaking down.
- Environmental Conditions: Factors like humidity, exposure to chemicals, and potential environmental hazards should inform your lubricant choice.
- Application Type: The nature of the movement (oscillating, rotational, etc.) within the fittings will determine the appropriate lubricant.
The Application of Fitting Lubrication
Proper application of lubricants is vital to achieving optimal performance. Follow these steps for effective fitting lubrication:
1. Clean the Fittings
Before applying lubricant, ensure that the fittings are clean. Remove any dirt, old lubricant, and debris to prevent contamination. A clean surface allows the new lubricant to adhere properly and perform effectively.
2. Choose the Right Lubrication Method
Depending on the fitting and lubricant type, choose an appropriate method of application:
- Brush Application: Useful for greases, allowing precise placement.
- Squeeze Tubes: Ideal for small amounts of lubricant.
- Automatic Lubricators: Best for continuous lubrication in larger or hard-to-reach fittings.
3. Apply the Lubricant Evenly
Ensure that the lubricant is applied evenly across the fitting surfaces. Uneven application can lead to inadequate lubrication and increased wear.
4. Monitor and Maintain
Regularly check the fittings for signs of wear or insufficient lubrication. Reapply lubricant as necessary to maintain performance.
Common Issues Caused by Inadequate Lubrication
Neglecting proper fitting lubrication can lead to several issues, including:
- Pitting: This occurs when surfaces wear down at different rates due to inadequate lubrication, causing surface degradation.
- Seizure: Insufficient lubrication may lead to overheating, causing the fitting to seize or fail altogether.
- Corrosion: Without the protective layer that lubricants provide, fittings are susceptible to rust and corrosion, impacting functionality.
- Increased Energy Consumption: Fittings that lack lubrication create higher friction, leading to more energy consumption and reduced efficiency.
Conclusion
In conclusion, fitting lubrication is a critical factor in maintaining the efficiency and longevity of fittings across various industries. By reducing friction, preventing corrosion, and enhancing overall reliability, proper lubrication can save businesses significant costs associated with downtime and repairs. Understanding the different types of lubricants available, the factors influencing their usage, and best practices for application are essential steps in optimizing your equipment's performance.
At fitsch.cn, we offer high-quality fittings and expert advice on lubrication strategies tailored to your specific needs. Make informed decisions about lubrication, and invest in the longevity and efficiency of your fittings today.