Micro Precision Injection Molding: Revolutionizing the Manufacturing Landscape
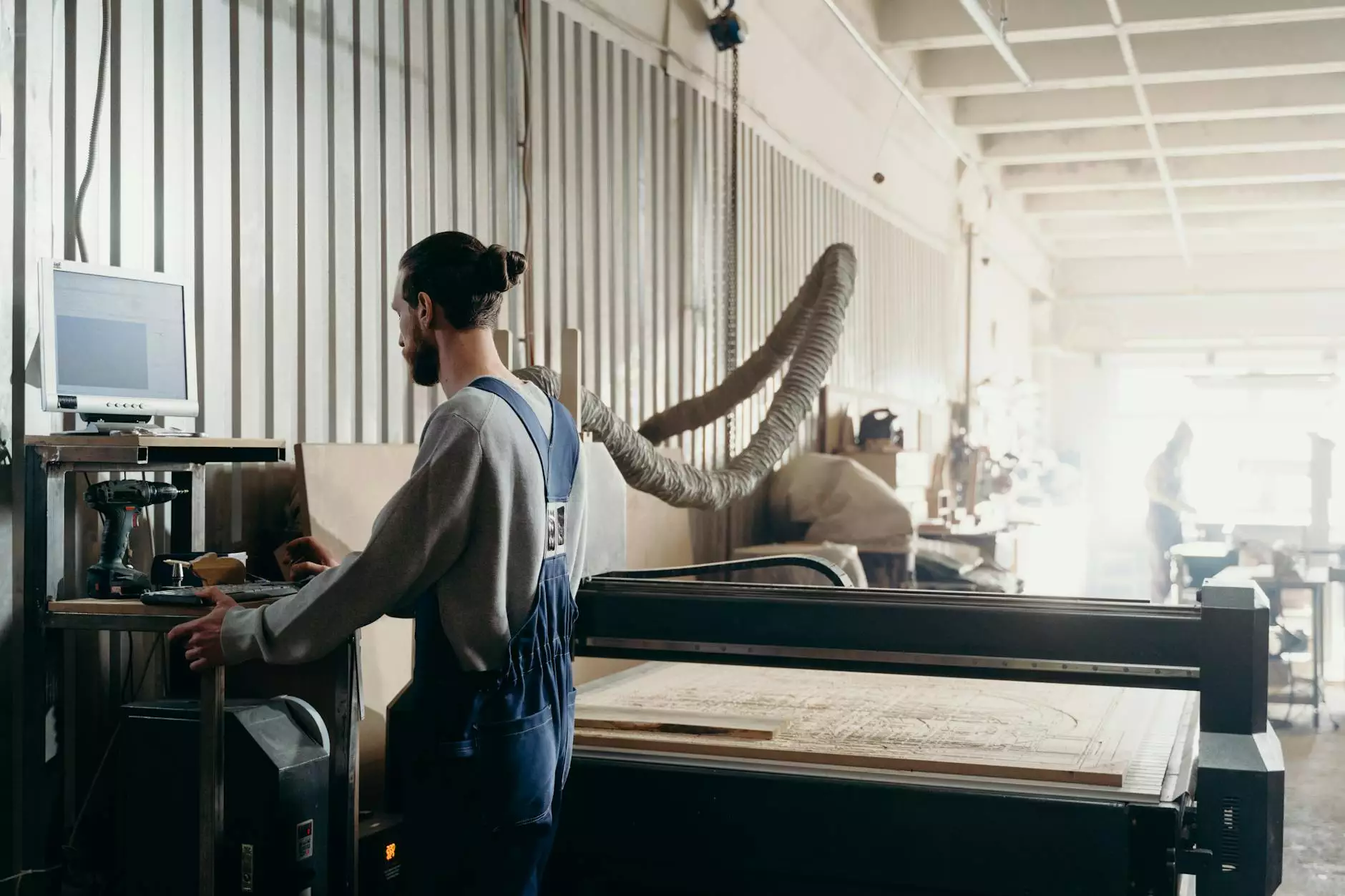
In today's rapidly evolving industrial world, micro precision injection molding stands at the forefront of innovation, particularly within the realm of metal fabrication. This cutting-edge technology is not just a trend but a transformative process that is shaping the future of manufacturing. In this article, we will delve into the intricacies of micro precision injection molding, its applications, advantages, and how companies like DeepMould.net are leading the charge in this exciting field.
Understanding Micro Precision Injection Molding
Micro precision injection molding is a specialized manufacturing process that involves injecting molten material into a mold cavity with extreme precision. This technique is primarily used to create small, intricate parts that require precise dimensions in various industries, including automotive, aerospace, electronics, and medical devices.
The Process Explained
The micro precision injection molding process entails several critical steps:
- Material Selection: The process begins with choosing the appropriate material, which can range from plastics to metals, depending on the application.
- Designing the Mold: High-precision molds are designed using advanced CAD software to ensure that all details and tolerances are met.
- Injection: The material is heated until it becomes molten and is injected into the mold under high pressure.
- Cooling: Once the mold is filled, it is cooled to solidify the material and form the precise component.
- Finishing: After cooling, the part is ejected from the mold, and any necessary finishing processes are applied to meet the required specifications.
Key Materials Used
Common materials used in micro precision injection molding include:
- Thermoplastics: Ideal for creating complex shapes and offering excellent durability.
- Metal Alloys: Used in applications requiring strength and thermal stability.
- Elastomers: These flexible materials are often used for seals and gaskets.
The Applications of Micro Precision Injection Molding
The applications of micro precision injection molding are vast and varied, impacting several key industries:
1. Automotive Industry
In the automotive sector, micro precision injection molding is employed to create small components such as gears, clips, and sensors that contribute to the functionality and efficiency of vehicles. The precision ensures that these parts fit perfectly, thereby enhancing performance.
2. Electronics Industry
Manufacturers of electronic devices rely heavily on this technology for producing intricate components like connectors and housings. The accuracy of the molding process allows for complex designs that are essential in modern electronics.
3. Medical Devices
In the medical field, precision is paramount. Micro precision injection molding is crucial for creating small components used in devices like syringes, catheters, and implantable devices. The ability to produce contamination-free parts ensures patient safety.
4. Aerospace Sector
The aerospace industry benefits from this technology by producing lightweight yet strong components that can withstand extreme conditions. Every ounce of weight savings can translate into significant fuel efficiency for aircraft.
Advantages of Micro Precision Injection Molding
The benefits of adopting micro precision injection molding in manufacturing are numerous:
- High Precision and Accuracy: This technology allows manufacturers to produce parts with tolerances of +/- 0.001 inches.
- Reduced Waste: The precision of the process results in minimal excess material, making it an environmentally friendly manufacturing solution.
- Cost-Effectiveness: Although the initial setup may be high, the efficiency and speed of the process lead to lower production costs in the long run.
- Enhanced Production Speed: With rapid cycles, manufacturers can produce large volumes of parts quickly, meeting market demands efficiently.
Challenges in Micro Precision Injection Molding
While the advantages are significant, there are also challenges to consider:
1. Equipment Costs
The machinery and tooling required for micro precision injection molding can be costly. However, investing in high-quality equipment is paramount to achieve the desired precision.
2. Expertise Required
Achieving the required precision mandates skilled technicians and engineers. Continuous training and upskilling are necessary to maintain high standards.
3. Material Limitations
Not all materials perform well in micro injection molding. Some materials may not flow correctly or may not solidify in a way that meets precision criteria.
Why Choose DeepMould.net for Micro Precision Injection Molding?
DeepMould.net stands as a beacon of excellence in the field of micro precision injection molding. Here’s why:
1. Cutting-Edge Technology
Using the latest machinery and techniques, DeepMould.net ensures that every project meets the highest precision standards, delivering exceptional quality parts.
2. Experienced Team
The skilled professionals at DeepMould.net have extensive industry experience, assuring clients of their capability to handle complex projects with ease.
3. Customized Solutions
DeepMould.net understands that no two projects are alike. They offer tailor-made solutions to meet specific client needs, ensuring maximum satisfaction.
4. Commitment to Sustainability
By employing techniques that minimize waste and optimize resources, DeepMould.net is dedicated to sustainable manufacturing practices.
Conclusion
The realm of micro precision injection molding is evolving, making it an indispensable element of modern manufacturing. Its applications span numerous industries, providing solutions that are not only efficient but also cost-effective and environmentally conscious. With leaders like DeepMould.net at the helm, the future of manufacturing looks promising, characterized by enhanced precision and innovative solutions that drive progress. By investing in micro precision injection molding, companies can elevate their production processes, satisfy consumer demand, and stay competitive in a rapidly changing market.